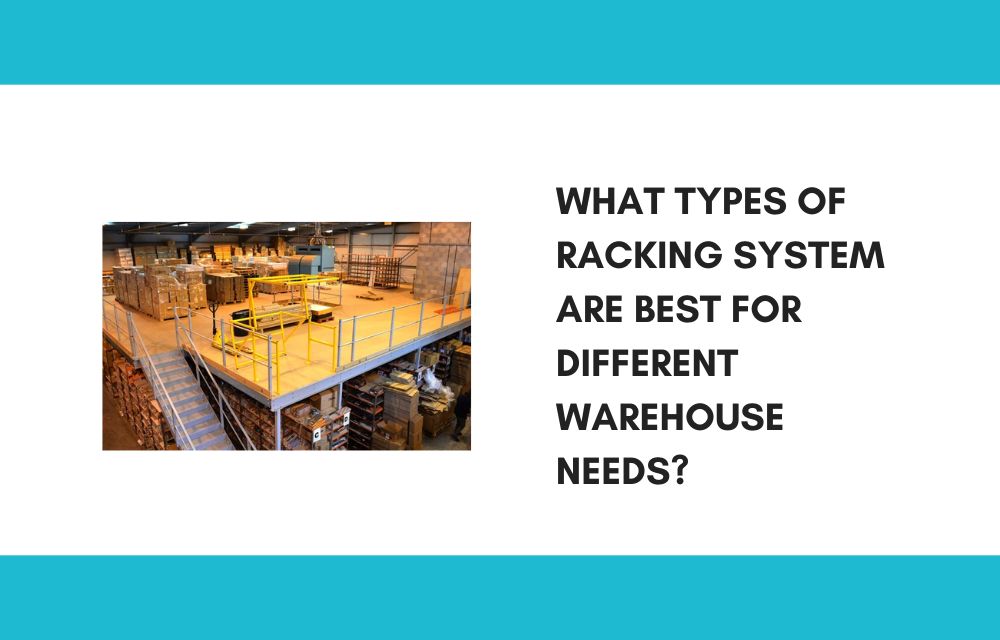
A well-organized warehouse is key to improving efficiency and productivity in any business. One of the most important parts of a warehouseโs organization is the racking system. Racking systems are designed to store goods in an organized way, making it easier for workers to access items quickly. The type of racking system you choose will depend on various factors such as the size of your warehouse, the types of products you store, and how frequently you need to access them. In this article, we will look at different types of racking system for warehouse and help you decide which one is best suited for your warehouse needs.
Why Choose the Right Racking System?
The Importance of a Good Racking System
Choosing the right racking system for your warehouse is essential for multiple reasons. A good racking system helps:
- Maximize Space: A well-planned racking system makes use of every available inch in your warehouse, increasing storage capacity.
- Improve Efficiency: With a proper racking system, workers can find items easily and move them quickly.
- Ensure Safety: A sturdy and organized racking system helps prevent accidents caused by items falling or being misplaced.
- Save Time and Money: When items are easy to locate, you reduce the time spent searching, improving overall efficiency and lowering operational costs.
Understanding Your Warehouse Needs
Before choosing a racking system, consider several factors:
- The types of products you store.
- The volume of products you need to store.
- How often you access the products.
- Available space in your warehouse.
- Safety considerations for both workers and products.
Once you have these factors in mind, you can better assess which type of racking system is ideal for your warehouse.
Different Types of Racking Systems and Their Benefits
1. Selective Racking System
What Is Selective Racking?
Selective racking is one of the most common racking systems used in warehouses. Itโs designed for easy access to every pallet stored on the shelves. In a selective racking system, pallets are placed on horizontal beams and can be accessed individually. This system is highly flexible and works well for a wide variety of products.
Benefits of Selective Racking
- Easy Access: Every pallet can be accessed directly without needing to move other items, making it ideal for warehouses that deal with various types of products.
- Cost-Effective: Selective racking systems are relatively inexpensive to install and require less space compared to other more complex systems.
- Flexible Layout: This system works well for warehouses with different types of products and varying inventory levels.
When to Use Selective Racking
If you need easy access to your products and have a wide variety of goods that change frequently, selective racking is a great option. It is commonly used in retail, distribution centers, and warehouses where stock is rotated regularly.
2. Drive-In and Drive-Through Racking Systems
What Is Drive-In and Drive-Through Racking?
Drive-in and drive-through racking systems allow forklifts to drive into the racks to store and retrieve goods. The key difference between the two systems is that in drive-in systems, the forklift drives into the racking from one side, while in drive-through systems, the forklift can enter from both sides.
Benefits of Drive-In and Drive-Through Racking
- High Density Storage: These systems allow you to store products more densely, making the most of available space.
- Last-In, First-Out (LIFO) Method: Both systems work well for products that donโt require frequent stock rotation and are stored in bulk.
- Improved Space Utilization: Drive-in and drive-through racking systems can store a large quantity of products in a smaller footprint, reducing wasted space.
When to Use Drive-In or Drive-Through Racking
These racking systems are ideal for storing large quantities of the same product in your warehouse. They work best in industries like food and beverage or pharmaceuticals, where products are stored in bulk and donโt need to be rotated as often.
3. Push-Back Racking System
What Is Push-Back Racking?
The push-back racking system is a high-density racking system that allows pallets to be stored on inclined rails. When a forklift adds a new pallet, the previous pallets are pushed backward. This system uses the “last-in, first-out” (LIFO) principle, meaning the most recently placed pallets are the first to be retrieved.
Benefits of Push-Back Racking
- Space Efficiency: Push-back racking makes efficient use of warehouse space by storing pallets in a compact arrangement.
- Higher Storage Density: It allows you to store more products in a smaller area compared to selective racking.
- Improved Access to Products: Even though pallets are pushed back, they are still relatively easy to retrieve.
When to Use Push-Back Racking
Push-back racking is ideal for warehouses that store multiple products in moderate quantities. This system works well in manufacturing and retail environments where stock needs to be rotated and high-density storage is a priority.
4. Cantilever Racking System
What Is Cantilever Racking?
Cantilever racking is designed for storing long or bulky items that are difficult to store on traditional pallet racks. This system has vertical columns with horizontal arms that extend to hold items such as pipes, timber, or furniture.
Benefits of Cantilever Racking
- Ideal for Bulky Items: Cantilever racking is perfect for storing long or irregularly shaped items such as steel rods, pipes, and wood beams.
- Easy to Load and Unload: Since there are no vertical obstructions, large or awkwardly shaped items are easy to place and remove from the racks.
- Highly Flexible: The system can be adjusted to accommodate items of varying sizes and weights.
When to Use Cantilever Racking
If your warehouse stores long or heavy items like furniture, steel beams, or pipes, then a cantilever racking system is ideal. It is commonly used in construction, manufacturing, and furniture storage industries.
5. Mezzanine Racking System
What Is Mezzanine Racking?
A mezzanine racking system adds a second level of storage to a warehouse. It involves building a raised platform within the warehouse, which can be used to store additional goods. This system helps businesses maximize vertical space without needing to expand the warehouseโs physical footprint.
Benefits of Mezzanine Racking
- Increased Storage Capacity: The mezzanine level adds extra storage space, which is especially helpful if you are running out of room on the ground level.
- Cost-Effective: Building upwards is generally more affordable than expanding horizontally by adding more warehouse space.
- Flexible Use: You can use the extra level for storage or for other warehouse functions like packaging or assembly.
When to Use Mezzanine Racking
Mezzanine racking is best used when you need extra storage but canโt expand your warehouse. It works well in e-commerce, retail, and small-scale manufacturing operations where space is at a premium.
6. Double-Deep Racking System
What Is Double-Deep Racking?
Double-deep racking involves placing pallets two-deep in a racking system, using a forklift to retrieve items from the back of the rack. Itโs similar to selective racking but allows you to store two pallets in the same space.
Benefits of Double-Deep Racking
- Higher Density Storage: Double-deep racking makes better use of available space by storing pallets two deep.
- Access to Multiple Products: While the back pallet is harder to reach, it can still be accessed easily with the right forklift.
When to Use Double-Deep Racking
Double-deep racking works well for warehouses that need to store large quantities of the same product and can use the last-in, first-out system.
Choosing the Best Racking System for Your Warehouse
1. Consider Available Space
The amount of space you have in your warehouse will influence the type of racking system you choose. If you have limited space, high-density options like push-back or drive-in racking might be ideal. If you have ample space and need to access products quickly, selective racking is a better option.
2. Think About the Type of Products
Consider the type of products you store. Bulky items like pipes or wood should be stored using cantilever racking, while smaller, high-turnover products are best stored using selective or push-back racking.
3. Frequency of Access
If you need to frequently access your products, choose a system like selective racking or drive-through racking. If you have less frequent access needs, systems like drive-in or push-back racking may work better.
4. Safety and Durability
Always consider the safety of your warehouse workers when choosing a racking system. The racking should be stable and durable to avoid accidents. Itโs important to regularly inspect racks for any signs of damage.
Conclusion
Choosing the right racking system for your warehouse is crucial for maximizing storage space, improving efficiency, and maintaining safety. Different racking systems offer unique benefits depending on your needs. By understanding the different types of racking systems and their advantages, you can select the one that best suits your warehouse.
Note:- To read more articles visit on ideaexpress.
Leave a Reply