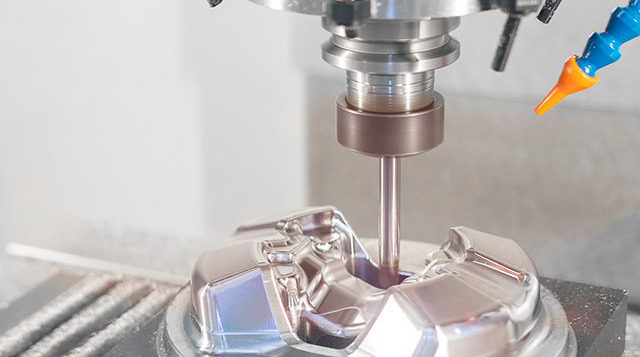
Introduction
The intersection of technology and healthcare has seen remarkable innovations, and one of the key drivers of this transformation is Medical CNC technology. In the medical field, CNC technology is used for the precise manufacturing of medical devices, implants, surgical instruments, and other essential products. By combining high-tech machinery with automated precision, Medical CNC enhances the accuracy, speed, and quality of manufacturing processes. This article delves into the significance of Medical CNC in healthcare, its applications, benefits, and the ways it is shaping the future of medical manufacturing.
What is Medical CNC?
At its core, Medical CNC refers to the use of CNC machines in the production of medical products. CNC technology is a method of automating and controlling machine tools through a computer program. The system interprets a digital design and translates it into physical motion on the machine, which can be used to cut, shape, mill, or carve various materials. CNC machining is highly regarded for its accuracy and ability to produce complex shapes, making it ideal for the medical field where precision is paramount.
In medical manufacturing, CNC machines can create highly detailed components for devices, implants, and tools with a degree of precision that is critical for patient safety and product functionality.
Applications of Medical CNC
1. Medical Implants
Medical implants, such as artificial joints, dental implants, and spinal implants, are critical components in modern healthcare. These implants must fit the body precisely and function seamlessly to ensure patient health and comfort. CNC technology allows manufacturers to create complex shapes and detailed features necessary for implants like hip replacements, knee joints, and dental implants. CNC machining ensures that these components fit the human anatomy precisely, minimizing complications and improving patient outcomes. The ability to customize implants further enhances the personal fit for each patient, reducing the risk of implant rejection or discomfort.
2. Surgical Instruments
Surgical instruments like scalpels, forceps, and scissors are essential for performing medical procedures safely and effectively. CNC machining allows for the mass production of surgical instruments with high precision, ensuring that each tool has the required sharpness, ergonomics, and durability. Moreover, the customization of tools to suit specific procedures or surgeons’ preferences is possible, enhancing the overall efficiency of surgeries. The use of high-quality materials, such as stainless steel or titanium, in CNC machining also ensures that the instruments are long-lasting and resistant to corrosion, making them ideal for use in sterile environments.
3. Prosthetics and Orthopedics
CNC technology has significantly transformed the field of prosthetics and orthopedics. Custom prosthetics, including artificial limbs, are made with CNC machines that can create parts designed to fit the unique dimensions and requirements of an individual patient. Whether itโs a prosthetic limb or a back support brace, CNC machines can produce these devices with high precision, ensuring comfort, mobility, and better alignment. In addition to custom prosthetics, orthopedic devices like braces and supports benefit from CNC technology, as it allows for the accurate molding of lightweight yet durable materials that provide optimal support.
4. Dental Products
CNC technology is widely used in the dental industry for the creation of highly accurate crowns, bridges, dentures, and orthodontic devices. With the advent of 3D scanning and CNC milling, dental labs can now produce dental products with perfect fit and function. For example, dental crowns can be milled to match a patientโs natural tooth structure, and orthodontic devices like braces can be made to align with the individualโs teeth precisely. The precision offered by CNC ensures better patient outcomes and contributes to overall dental care.
5. Rapid Prototyping
The development of new medical devices often involves the creation of prototypes for testing and evaluation. CNC machining plays a key role in rapid prototyping, allowing manufacturers to quickly produce accurate models of medical devices for trials. This capability reduces the time required to move from design to production, accelerates innovation, and makes it easier to evaluate new materials, shapes, and functions. For instance, in the development of new medical tools or implants, rapid prototyping allows researchers to identify any potential design flaws or improvements before moving forward with mass production.
Benefits of Medical CNC
1. Precision and Accuracy
In the medical field, accuracy is of paramount importance, and CNC machines excel in this area. These machines can produce parts and components with tolerances as tight as 0.001 mm. This degree of precision ensures that medical devices, such as implants and surgical instruments, function exactly as intended, reducing the risk of complications or failure. For example, the precise fitting of an implant in a patientโs body ensures better alignment and less chance of injury, infection, or discomfort.
2. Customization
One of the most significant benefits of CNC technology in medicine is the ability to customize medical products. Medical implants, prosthetics, and dental devices are often tailored to fit the specific anatomical features of individual patients. CNC machining makes this customization possible by creating highly detailed and personalized products that improve the overall patient experience. Whether it’s a custom-made knee replacement or a dental crown that matches the shape of a patientโs natural teeth, CNC technology provides the flexibility to meet unique medical needs.
3. Increased Efficiency
CNC machines significantly increase manufacturing efficiency. Since these machines are automated, they can operate 24/7, producing medical components at a faster rate than traditional methods. Moreover, CNC machining reduces human error, ensuring consistency and accuracy across multiple production runs. The efficiency of CNC machines reduces production lead times and allows manufacturers to meet the growing demand for medical products, especially in cases of medical emergencies, pandemics, or disasters.
4. Consistency and Repeatability
Medical products must meet strict regulatory standards to ensure patient safety, and consistency is essential in this regard. CNC machines offer unparalleled consistency, ensuring that every product produced matches the same specifications and quality. Unlike manual methods, which can introduce variations in size, shape, and finish, CNC machines maintain uniformity across all components, reducing the risk of defective products.
5. Reduced Human Error
Manual manufacturing processes are prone to human errors that can lead to defects or inefficiencies. CNC technology reduces this risk by automating the entire process. Once the design is input into the computer system, the CNC machine follows the programmed instructions with minimal human intervention. This leads to more accurate and reliable production, especially for medical devices that require high levels of precision.
6. Cost-Effectiveness
Although the initial investment in CNC machinery can be high, the long-term savings it offers are significant. CNC machines reduce labor costs, as fewer skilled operators are needed to monitor the process. Additionally, the automation and efficiency of CNC systems lead to reduced waste and material costs. In the medical field, where product quality must remain high while maintaining cost competitiveness, CNC machining plays an essential role in keeping manufacturing costs under control.
The Impact of Medical CNC on Healthcare
1. Improved Patient Care
The precision and customization that CNC technology provides contribute to better patient outcomes. By enabling the production of implants, prosthetics, and surgical instruments that are tailored to individual needs, CNC ensures that patients receive the most appropriate and comfortable treatments. This reduces the risk of complications and enhances the overall quality of care.
2. Advancing Medical Innovation
Medical CNC machining has been pivotal in advancing innovation in medical device development. The ability to create prototypes rapidly and refine them using CNC technology accelerates the development of new devices and treatments. This continuous innovation is crucial in addressing evolving medical challenges and improving healthcare across the world.
3. Regulatory Compliance
Medical devices must meet stringent regulatory requirements set by governing bodies such as the FDA (U.S. Food and Drug Administration) and the CE (Conformitรฉ Europรฉenne). CNC technology plays a crucial role in ensuring that products meet these high standards of safety and performance. The precision and repeatability of CNC machining help manufacturers comply with these regulations, ensuring that their products are safe for patient use.
Conclusion
Medical CNC technology has proven to be a transformative force in the healthcare industry, offering a wide range of benefits that improve the manufacturing process for medical devices and products. From implants and surgical instruments to customized prosthetics and dental products, CNC machining plays a vital role in creating high-quality, precision-driven solutions that directly impact patient care. As the medical field continues to evolve, the role of CNC technology will only expand, driving further innovation, efficiency, and customization in healthcare manufacturing. The future of medical devices and implants is undoubtedly intertwined with the ongoing advancements in CNC technology, ensuring better outcomes for patients around the world.
Leave a Reply