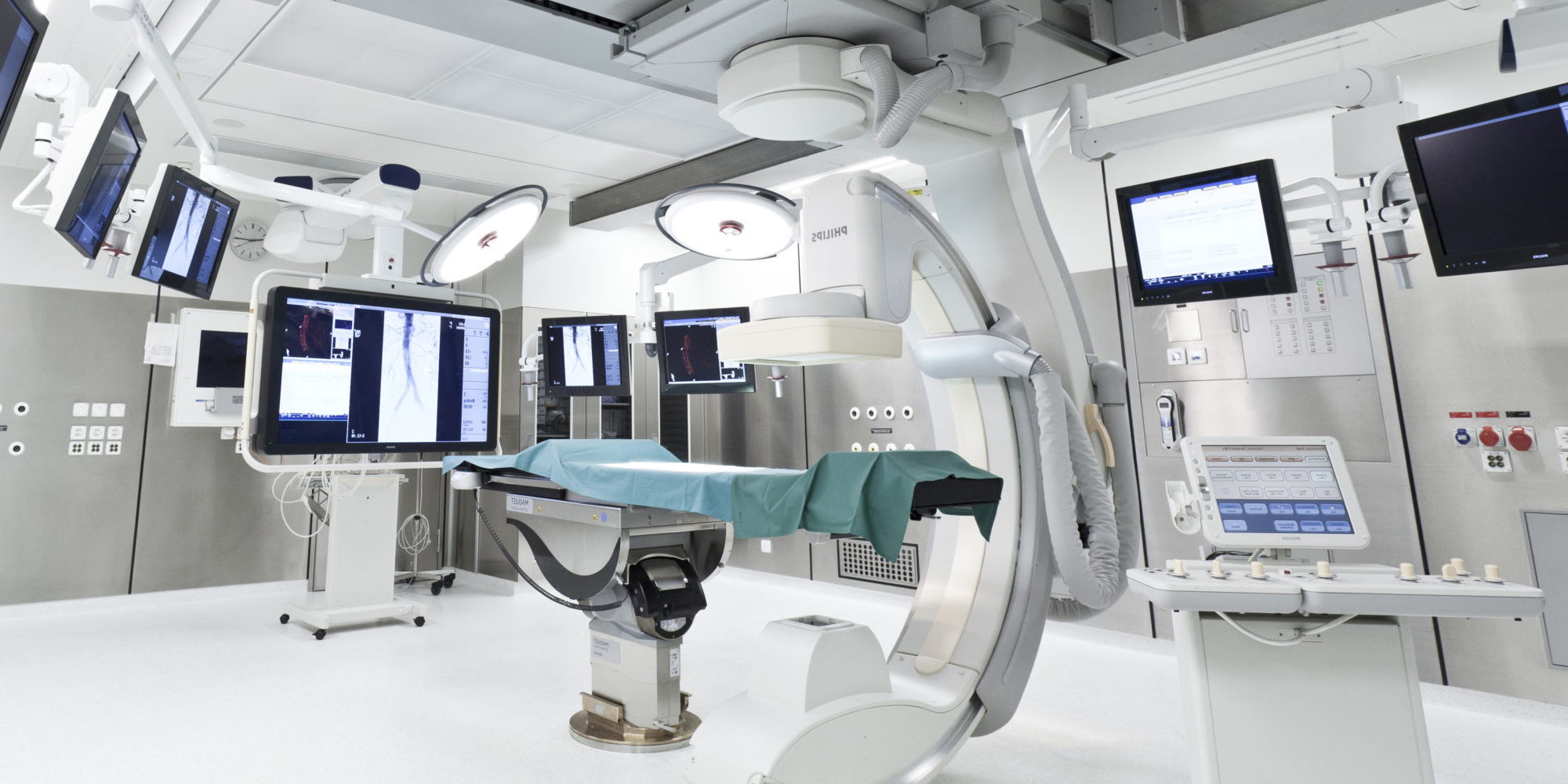
In the healthcare industry, precision and accuracy are not just important—they are vital. The devices and tools used in medical treatments, whether they are implants, surgical instruments, or diagnostic equipment, must meet the highest standards of quality and reliability. Medical CNC, or Computer Numerical Control machining, plays a critical role in ensuring that these devices are produced with the exacting precision required for patient safety and treatment efficacy.
CNC machines are used to automate the production process of medical devices and parts, ensuring that even the most intricate components are created consistently and with tight tolerances. This article explores the role of CNC machining in the medical field, its benefits, applications, and how it is transforming the production of medical devices.
What is CNC Machining?
CNC machining refers to a manufacturing process that uses computerized controls to operate machinery. The primary advantage of CNC over traditional manual machining is the ability to produce parts with high precision and consistency. CNC machines are equipped with advanced software that reads digital designs and turns them into physical parts, making the process automated and reducing human error.
In the medical field, CNC machining is used to create a variety of products such as surgical instruments, dental implants, orthopedic components, and diagnostic tools. The ability to consistently produce parts with tight tolerances is essential in medical device manufacturing, where even the smallest error can result in safety risks for patients.
How CNC Machines Operate
CNC machines operate using a process that begins with a CAD (Computer-Aided Design) model. This digital design specifies the exact dimensions and features required for the part. Using CAM (Computer-Aided Manufacturing) software, the design is converted into a set of instructions that the CNC machine follows to manufacture the part.
CNC machines operate through various operations like cutting, drilling, milling, and turning, depending on the specific device being produced. These machines can handle a wide range of materials, including metals, plastics, and ceramics, which are commonly used in medical devices.
Benefits of CNC Machining in Medical Device Manufacturing
The use of CNC machining in medical device production offers several advantages over traditional manufacturing methods. These benefits ensure that medical devices are produced efficiently, precisely, and with the highest quality standards.
1. Precision and Accuracy
One of the most significant advantages of CNC machining in the medical field is its ability to produce parts with extremely high precision. Medical devices often have strict tolerance requirements, and even the slightest deviation can compromise the device’s functionality or safety. CNC machines can produce parts with tolerances as tight as a few micrometers, ensuring that every piece meets the exact specifications.
2. Consistency and Reproducibility
CNC machining is an automated process, meaning that once the program is set, it can produce identical parts consistently. This level of repeatability is crucial in medical device manufacturing, as it ensures that large batches of the same part are produced with the same level of quality and precision.
3. Customization for Patients
Many medical devices, such as implants, need to be customized to fit individual patients’ specific anatomy. CNC machining is ideal for this type of work, as it allows for the production of custom-made parts with high precision. For example, CNC machines can create implants or prosthetics tailored to a patient’s unique measurements, improving the outcome of medical treatments and surgeries.
4. Complex Geometries and Intricate Designs
Medical devices often require intricate designs and complex geometries that would be difficult to achieve using traditional manufacturing methods. CNC machines excel in producing complex features, including small holes, fine threads, or detailed surface textures, which are often found in medical components. This allows manufacturers to create cutting-edge medical devices with advanced designs.
5. Material Versatility
CNC machines can work with a wide variety of materials, many of which are commonly used in medical devices. These include metals like stainless steel and titanium, biocompatible polymers, ceramics, and composites. This versatility ensures that manufacturers can choose the most appropriate material for each medical device while meeting biocompatibility and durability standards.
6. Faster Turnaround Times
The automation of CNC machining significantly speeds up the manufacturing process compared to traditional methods. Once the machine is programmed, it can operate continuously, reducing the time required to produce parts. Faster production times can help manufacturers meet deadlines, especially in industries where rapid prototyping and quick responses to market demands are essential.
Applications of CNC Machining in the Medical Field
CNC machining plays a vital role in producing a wide range of medical devices, from high-precision surgical tools to custom-made implants. Here are some of the key applications:
1. Surgical Instruments
Surgical instruments, such as forceps, scalpels, scissors, and clamps, require extreme precision to ensure safety during operations. CNC machining is used to manufacture these tools with tight tolerances and sharp edges, ensuring they function optimally in delicate surgeries. The accuracy of CNC machines is particularly important for instruments used in minimally invasive surgeries, where small margins for error exist.
2. Medical Implants
Medical implants, such as artificial joints, dental implants, and pacemakers, need to fit seamlessly into the body. CNC machining allows for the production of implants that match a patient’s unique anatomy. Whether it’s a custom-made hip replacement or a dental crown, CNC machines can create implants with the required shape, size, and fit to ensure a successful outcome.
3. Orthopedic Devices
Orthopedic devices like bone plates, screws, and spinal implants require the highest level of precision and strength. CNC machining ensures that these components are manufactured to meet the exact specifications required for the surgical procedures. The process also allows for the creation of personalized components based on a patient’s anatomy, improving the performance of these devices.
4. Dental Devices
The dental industry also benefits greatly from CNC machining. CNC machines are used to produce custom dental implants, crowns, bridges, dentures, and orthodontic devices. These components must fit perfectly in a patient’s mouth, and CNC machining provides the necessary precision to ensure a comfortable and effective fit.
5. Prosthetics
CNC machining is commonly used in the production of prosthetic limbs and other assistive devices. Customization is key in prosthetics, as each device must be tailored to the patient’s body. CNC machining enables the creation of prosthetic components that fit comfortably and function effectively, improving the quality of life for patients with disabilities.
6. Medical Equipment Parts
In addition to medical devices used directly on patients, CNC machining is used to produce parts for medical diagnostic and treatment equipment. These components are often complex, requiring precision for optimal performance. CNC machines are used to create parts for equipment like MRI machines, CT scanners, and ultrasound devices, ensuring that these tools function effectively in a medical setting.
The Future of CNC Machining in Medical Device Manufacturing
As technology advances, CNC machining in the medical field will continue to evolve. The development of multi-axis CNC machines, which allow for more complex movements, and additive manufacturing (3D printing), which can work in tandem with CNC machining, will enable the production of even more advanced medical devices. The ability to combine different manufacturing processes will result in even more customized and efficient solutions for the healthcare industry.
Furthermore, advancements in robotics and artificial intelligence (AI) will increase the automation and accuracy of CNC machining. AI can help optimize machining processes, predict potential issues, and improve overall manufacturing efficiency, resulting in better products and faster turnaround times.
Conclusion
CNC machining has become an indispensable part of medical device manufacturing, offering precision, speed, and customization that traditional methods cannot match. Whether for creating surgical instruments, implants, or diagnostic equipment, CNC machining ensures that medical devices meet the exacting standards required for patient safety and effectiveness.
With its ability to produce complex designs, handle a variety of materials, and provide consistent results, CNC machining will continue to play a critical role in shaping the future of the medical industry. As technology advances, the role of CNC in medical device manufacturing will expand, offering even greater precision, customization, and efficiency, ultimately improving patient outcomes and the quality of healthcare worldwide.
Leave a Reply