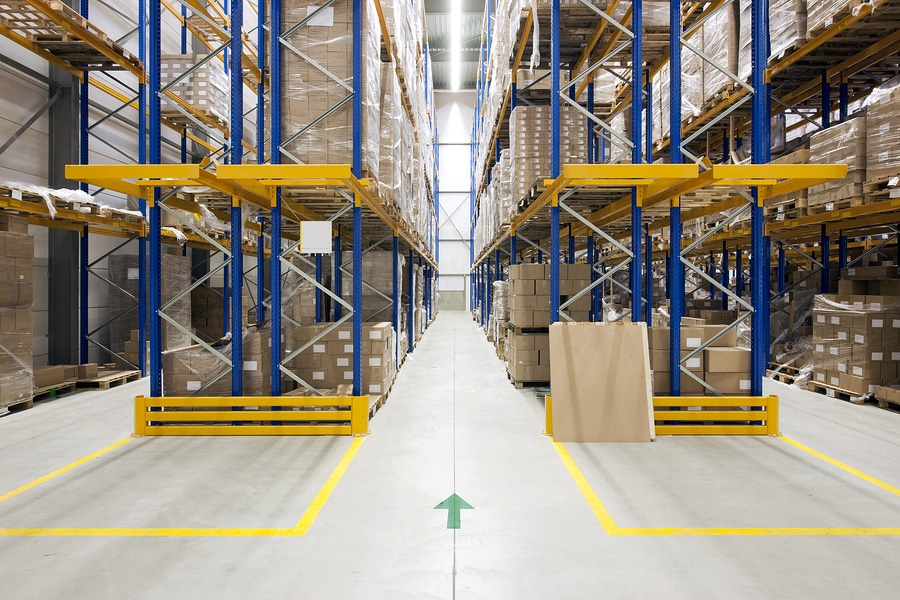
In small warehouses, the smallest inch matters. Thus, managing inventory and ensuring optimum accessibility and efficiency are essentials in making sure that operations will not come to a halt. This most efficient way of optimizing the utilization of small warehouses would be achieved through a properly planned racking system. Whether you run a stockroom for a retailing enterprise or a relatively small-scale distribution center, it can significantly make its operations more structured, easy to access, and streamlined.
One of the challenges is the small warehouse space needed to organize inventory, especially in the case of growing product lines or increased seasonal stock. Just available space doesn’t offer enough for a long-term effective means of storing and retrieving goods. Inadequate tools and systems can lead to inefficient ways of managing, and time can be wasted in terms of disorganization or lost revenue.
However, with the proper racking system, all these issues can be solved. The beauty of an installed racking system is that it can convert an otherwise cramped storage space into a highly functional and well-organized space. Here’s how:
1. Maximizing Vertical Space
This means using vertical space, not having items or products on the floor, as well as inefficient shelving units in a small warehouse. Rather, racking systems can stack up products towards the ceiling height of your warehouse. The system will result in an increased storage area and fewer products scattered here and there in your warehouse while maximizing every square foot.
For example, multiple levels of pallet racking or vertical racking systems can store goods that allow the smaller goods to be kept higher up to give more floor space for the bulkier stock or the more frequently accessed stock. This vertical storage maximizes the available area; it is especially useful where the floor space is minimal within a small facility.
2. Better Organization and Layout
A well-planned racking system also optimizes organization. Racking systems help streamline the workflow by categorizing products, combining similar items, and dedicating areas for different types of products. This, in turn, increases picking efficiency, minimizes the amount of time spent looking for products, and reduces the number of misplaced items.
For small warehouses, the racking system can be developed based on the specific flow of the goods. For instance, a flow-racking system holds products in such a manner as to ensure the ones placed first are the ones to be picked, which is excellent, particularly for perishable and time-sensitive items.
In addition, flexible racking systems allow for adjustments in different types and sizes of products. Shelves could be adjusted according to what changes in the inventory list; therefore, the system adapts to the requirements of the warehouse rather than costly redesigns or replacements.
3. Increased Accessibility
A good racking system must enhance access in the warehouse in any case, but more precisely, in crowded smaller warehouses, at a rate that affects the acquisition of access to the product in small warehouses. An ideal warehouse must ensure that high-demand stock products are within easy access so that low-demand ones are behind.
For example, with mobile or sliding racking systems, racks can be pushed aside to create temporary aisles and workers may access several rows of inventory without having to reach or stretch across multiple racks. The result is that employees will easily find and retrieve the right products without having to spend too much time moving around obstacles or squeezing through narrow spaces.
Having well-defined aisles in the warehouse, with accurate widths and racking heights, allows employees to travel comfortably through the warehouse and increases accessibility and safety within the premises.
4. Increased Density of Inventory
In small warehouses, every inch of storage space should be used effectively to maximize inventory density. Racking systems are designed to keep items in compact, organized units that reduce wasted space between goods. This enables the warehouse to hold more stock without increasing its physical footprint.
For example, double-deep racking systems allow two pallets of inventory to be stored in one rack position. This increases the density of the warehouse while still keeping it organized and accessible. Even in very tight spaces, clever designs such as cantilever racking or mobile shelving can help store all types of inventory in a smaller area while maintaining safety standards.
5. Flexible Design for Changing Needs
Small warehouses change fast, sometimes due to seasonal fluctuations in stock and sometimes because the nature of the products stored is changing. Hence, a flexible racking system is needed. Racking systems also have to be scalable and easy to adapt to the changing needs of the warehouse for any business.
For example, an adjustable shelving unit that can hold different sizes of stock or modular systems that can be added and reconfigured when inventory changes; therefore, as your business expands, the racking system will have to expand, keeping an organized small warehouse efficient without requiring setting up a whole new one.
6. Labor Efficiency Optimization
A racking system properly installed enhances labor efficiency greatly. In a warehouse, where employees do not have to dig around for products or traverse the store’s jumble of inventory, orders can be picked and packed much more efficiently. This efficiency is the most crucial aspect of any small warehouse since each minute saved could mean the difference between a big and small operation.
The ergonomic design of racking systems also minimizes workers’ physical strain. Due to their adjustable heights and easy-to-reach shelves, with rows visible, they are less prone to getting tired from bending, stretching, or lifting heavy stuff. Thus, it decreases the number of injuries at the workplace and maximizes operations performance.
Conclusion
For small warehouses, a well-designed racking system is not just an investment in storage but a game-changer in efficiency, organization, and space utilization. Racking systems help maximize vertical space, improve accessibility, and increase inventory density, transforming a cramped warehouse into a highly functional and efficient operation.
The most fitting racking system can still help a small warehouse achieve better productivity, safe working conditions, and smoother workflow. From managing small distribution centers to compact retail stockrooms, an efficient racking system installation is perhaps the best means of maximizing space use and getting more out of your warehouse.
Leave a Reply