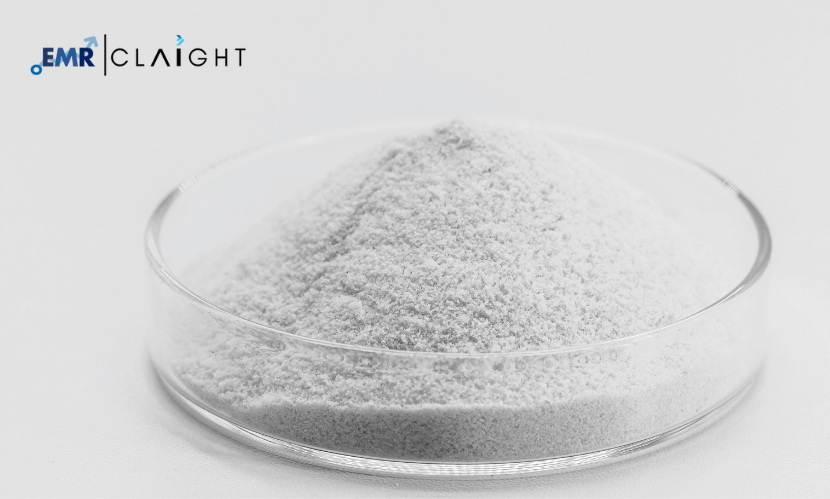
Magnesium phosphate is a crucial compound with widespread applications in industries such as agriculture, food, healthcare, and construction. Known for its role as a fertiliser, dietary supplement, and cement additive, magnesium phosphate is valued for its chemical stability and versatile properties. Establishing a magnesium phosphate manufacturing plant requires efficient production methods, quality assurance, and adherence to environmental and safety regulations. This article provides a detailed guide on the production processes, necessary equipment, and considerations for launching a successful magnesium phosphate manufacturing facility.
Understanding Magnesium Phosphate
Magnesium phosphate is an inorganic compound used extensively in agriculture as a fertiliser, in food as a dietary supplement, and in construction as a component of special cement. It is prized for its nutrient content, particularly in enhancing soil fertility, and its chemical properties, such as setting time and strength when used in construction materials.
Get a Free Sample Report with Table of Contents@ https://www.expertmarketresearch.com/prefeasibility-reports/magnesium-phosphate-manufacturing-plant-project-report/requestsample
Key Processes in Manufacturing
- Raw Material Preparation
- The primary raw materials include magnesium oxide or magnesium hydroxide and phosphoric acid. These materials are tested for quality and compatibility before processing.
- Reaction Process
- Magnesium and phosphate compounds undergo a controlled chemical reaction to form magnesium phosphate. Reaction conditions, such as temperature and pH, are carefully managed to optimise yield.
- Filtration and Drying
- The reaction mixture is filtered to remove impurities and then dried to obtain the desired form of magnesium phosphate, such as powder or granules.
- Granulation (Optional)
- For certain applications, the dried magnesium phosphate is granulated to create uniform particles, ensuring ease of application and distribution.
- Quality Testing
- The final product is subjected to rigorous testing to ensure it meets industry standards for purity, stability, and performance.
- Packaging and Storage
- The magnesium phosphate is packaged in appropriate containers to maintain quality during storage and transportation.
Essential Equipment for a Manufacturing Plant
Setting up a magnesium phosphate manufacturing plant requires specialised equipment for efficient production. Key equipment includes:
- Reactors: For controlled chemical reactions between magnesium and phosphate compounds.
- Filtration Systems: To separate impurities from the reaction mixture.
- Drying Units: For removing moisture and achieving the desired consistency.
- Granulators: For creating uniform granules suitable for various applications.
- Quality Testing Instruments: For analysing chemical composition, stability, and performance.
- Packaging Machines: For sealing and labelling containers with the finished product.
Designing the Plant Layout
An efficient plant layout ensures streamlined operations and compliance with safety standards. Key considerations include:
- Raw Material Storage: Secure areas for storing magnesium and phosphate compounds.
- Processing Zones: Dedicated sections for reaction, filtration, drying, and granulation.
- Quality Control Laboratory: Equipped for testing raw materials and finished products.
- Packaging and Labelling Areas: Automated systems for sealing and branding products.
- Waste Management Systems: Facilities for handling and treating by-products responsibly.
Quality Control in Manufacturing
Maintaining consistent quality is critical in magnesium phosphate production. Key quality control practices include:
- Raw Material Testing: Verifying the purity and compatibility of magnesium and phosphate compounds.
- Process Monitoring: Ensuring optimal reaction conditions, such as temperature and pH.
- Product Testing: Evaluating the final productβs physical and chemical properties.
- Packaging Inspection: Checking for secure seals and accurate labelling.
Regulatory and Licensing Requirements
Establishing a magnesium phosphate manufacturing plant involves compliance with various industry and environmental standards. Key requirements include:
- Chemical Safety Certifications: Adherence to regulations for handling and storing hazardous materials.
- Environmental Clearances: Managing emissions, waste, and effluents responsibly.
- Labelling Compliance: Providing accurate product information, including safety precautions.
- Workplace Safety Regulations: Ensuring the safety of workers through proper training and protocols.
Applications of Magnesium Phosphate
Magnesium phosphate is a versatile compound with applications across various industries:
- Agriculture: Used as a fertiliser to enhance soil fertility and crop yield.
- Food Industry: Incorporated into dietary supplements for its magnesium content.
- Healthcare: Employed in pharmaceuticals for treating magnesium deficiencies.
- Construction: Used as a setting agent in magnesium phosphate cements for specialised applications.
- Industrial Applications: Applied in water treatment and chemical manufacturing processes.
Sustainability in Manufacturing
Sustainability is a key focus in magnesium phosphate production. Measures to enhance sustainability include:
- Eco-Friendly Processes: Using efficient chemical reactions that minimise waste and energy consumption.
- Waste Recycling: Repurposing by-products for secondary applications, such as animal feed or soil conditioners.
- Emission Control: Implementing advanced technologies to reduce harmful emissions.
- Energy Efficiency: Adopting energy-saving equipment in drying and granulation processes.
Market Trends and Opportunities
The magnesium phosphate market is expanding due to its versatile applications and growing demand in various industries. Key trends include:
- Growth in Sustainable Agriculture: Increasing use of magnesium phosphate fertilisers to support eco-friendly farming practices.
- Rising Demand in Dietary Supplements: Expanding health awareness drives demand for magnesium-enriched supplements.
- Innovation in Construction Materials: Development of advanced magnesium phosphate cements for specialised applications.
- Global Expansion: Higher adoption in emerging markets driven by industrialisation and agricultural development.
Challenges in the industry include:
- Raw Material Costs: Managing fluctuations in the prices of magnesium and phosphate compounds.
- Regulatory Compliance: Adapting to stringent environmental and safety regulations.
- Market Competition: Differentiating products through innovation and consistent quality.
By adopting advanced production techniques, ensuring stringent quality control, and embracing sustainable practices, manufacturers can establish a successful magnesium phosphate production facility to cater to the growing demand across diverse industries.
Leave a Reply