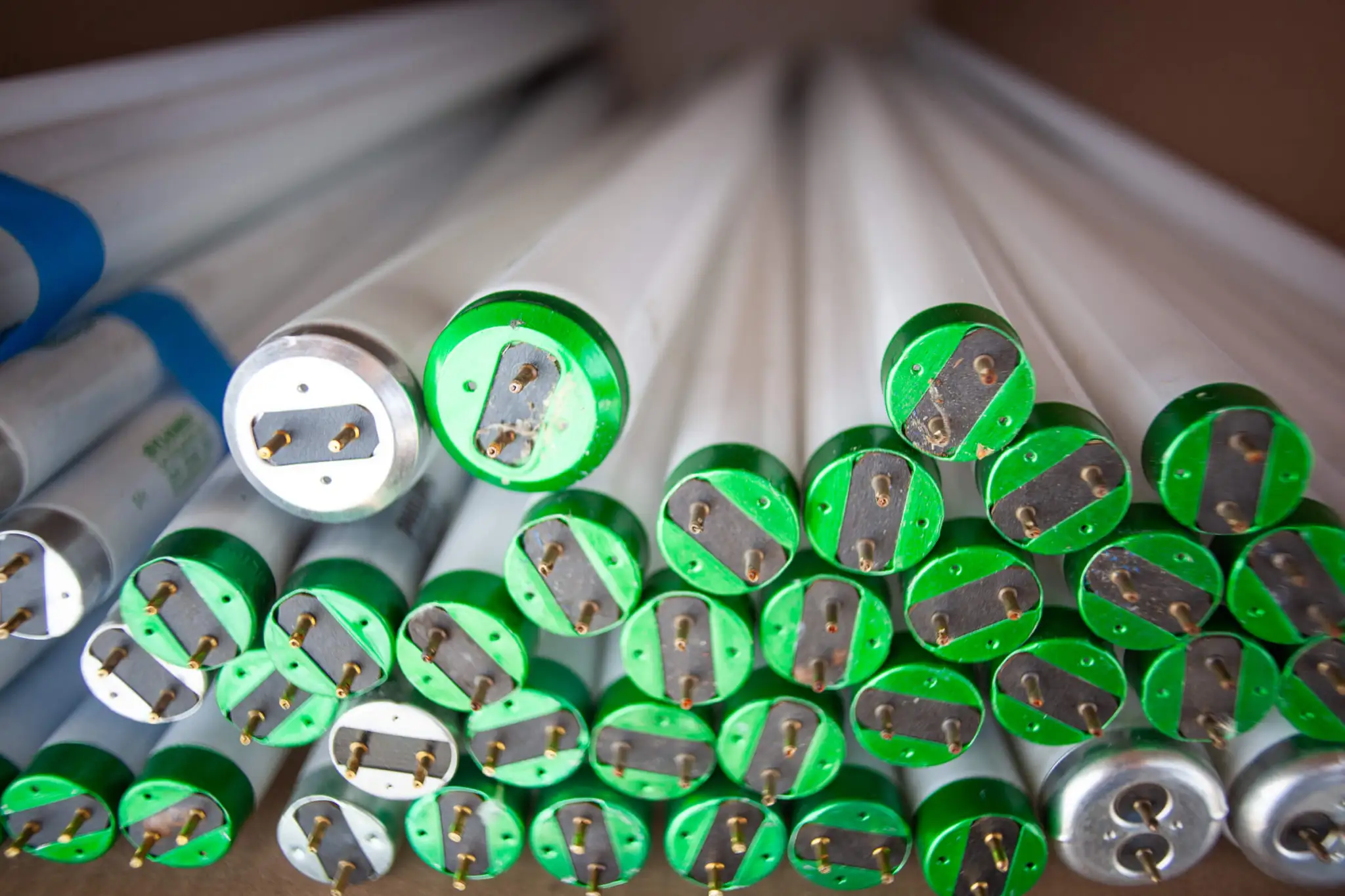
What Are Ballasts and Their Role in Lighting Systems
Ballasts are crucial components in lighting systems, especially fluorescent and high-intensity discharge (HID) lamps. They regulate the electrical current to ensure consistent light output while preventing overheating or burnout. Acting as a stabilizer, ballasts enable lighting systems to operate efficiently and safely.
Lighting systems have evolved significantly over the decades, but ballasts remain integral to both traditional and modern systems. Despite technological advancements like LED lights, millions of ballasts are still in use globally, making their proper disposal and recycling an important environmental concern.
Types of Ballasts: PCB and Non-PCB Variants
PCB Ballasts: The Environmental Hazard
PCB (polychlorinated biphenyl) ballasts were widely used in lighting systems until the late 1970s. These ballasts contain harmful chemicals known for their durability but also for their toxic environmental and health impacts. PCB contamination can persist in ecosystems, affecting soil, water, and wildlife for decades.
Non-PCB Ballasts: A Safer Alternative
As awareness of PCB hazards grew, non-PCB ballasts emerged as a safer alternative. These ballasts are free of toxic chemicals, making them less hazardous to the environment. They are manufactured with environmentally friendly materials, making their recycling more feasible and less damaging.
Understanding Non-PCB Ballasts
Benefits of Non-PCB Ballasts in Modern Lighting
Non-PCB ballasts offer numerous advantages over their PCB counterparts. These include:
- Reduced environmental toxicity.
- Easier recycling due to the absence of hazardous substances.
- Compliance with modern environmental regulations.
Switching to non-PCB ballasts supports global sustainability goals, helping reduce the ecological footprint of lighting systems.
Common Materials in Non-PCB Ballasts
Non-PCB ballasts are often made from materials like aluminum, steel, and copper. These metals are recyclable and retain value, making non-PCB ballasts an ideal candidate for circular economy practices.
The Importance of Recycling Non-PCB Ballasts
Reducing Landfill Waste Through Recycling
Recycling non-PCB ballasts prevents them from ending up in landfills, where their valuable materials would be wasted. Given the global push to reduce landfill usage, recycling programs can significantly reduce environmental pollution.
Energy Conservation Benefits of Non-PCB Ballast Recycling
Recycling materials like aluminum and copper consumes significantly less energy than extracting raw materials. By recycling non-PCB Ballast recycling, industries can conserve energy, reduce emissions, and contribute to more sustainable manufacturing practices.
Non-PCB Ballast Recycling Processes
Collection and Sorting of Non-PCB Ballasts
Effective recycling starts with proper collection and sorting. Businesses and facilities can collaborate with recycling centers to ensure non-PCB ballasts are separated from other waste, streamlining the recycling process.
Mechanical and Chemical Recycling Techniques
Once collected, non-PCB ballasts are processed using either mechanical or chemical recycling methods:
- Mechanical Recycling: Involves dismantling and shredding the ballast to recover metals and other components.
- Chemical Recycling: Uses solvents and heat to extract reusable materials from the ballast’s structure.
Ensuring Safety and Compliance During Recycling
Recycling facilities must follow strict safety and environmental regulations to handle and process ballasts responsibly. Proper training and certifications help workers avoid exposure to harmful substances and maintain compliance.
Challenges in Non-PCB Ballast Recycling
Market Limitations and Awareness
A lack of awareness about the recyclability of non-PCB ballasts often limits recycling rates. Businesses and consumers may not understand the environmental benefits or the processes involved.
Technical Barriers in Recycling Processes
Despite advancements, recycling non-PCB ballasts presents technical challenges. These include:
- Difficulty in dismantling ballasts with intricate designs.
- The need for specialized equipment to recover materials efficiently.
Solutions and Innovations in Non-PCB Ballast Recycling
Policy Frameworks and Incentives
Governments can promote recycling by implementing supportive policies and incentives, such as tax breaks or grants for businesses that participate in recycling programs.
Advanced Recycling Technologies
Innovations like automated sorting systems and high-efficiency shredders are making ballast recycling more effective and cost-efficient. These technologies can recover more materials while reducing processing time.
Economic Impacts of Recycling Non-PCB Ballasts
Creating Jobs and Business Opportunities
Recycling industries generate employment opportunities in collection, processing, and manufacturing. Communities benefit from job creation, while businesses profit from selling recycled materials.
Cost Savings for Manufacturers and Municipalities
Recycled materials from non-PCB ballasts are often cheaper than raw materials. Municipalities also save on landfill costs by diverting waste to recycling programs.
How Recycling Supports Sustainability Goals
Aligning with Global Environmental Targets
Recycling non-PCB ballasts aligns with international environmental agreements like the Paris Agreement, which aims to reduce greenhouse gas emissions and promote sustainable practices.
Promoting Circular Economy Practices
By recycling non-PCB ballasts, industries support a circular economy where materials are reused rather than discarded. This reduces the demand for raw material extraction and minimizes waste.
Best Practices for Non-PCB Ballast Recycling
Collaboration Among Stakeholders
Effective recycling requires collaboration between manufacturers, recyclers, and governments. Joint initiatives can improve recycling rates and reduce environmental impacts.
Educating Consumers and Businesses
Public awareness campaigns can encourage consumers and businesses to prioritize recycling. Education initiatives can also provide practical guidance on identifying and disposing of non-PCB ballasts.
Case Studies of Successful Non-PCB Ballast Recycling Programs
Industry-Led Initiatives
Major corporations in the lighting industry have launched recycling programs to manage ballast waste. These initiatives demonstrate the feasibility and benefits of large-scale recycling efforts.
Community-Driven Recycling Efforts
Grassroots movements and local recycling programs have successfully engaged communities in recycling non-PCB ballasts, showcasing the power of collective action.
Frequently Asked Questions (FAQs)
Why is recycling non-PCB ballasts important for sustainability?
Recycling prevents valuable materials from going to waste and reduces environmental pollution, supporting sustainability goals.
What are the key steps in the non-PCB ballast recycling process?
The process includes collection, sorting, dismantling, and material recovery using mechanical or chemical techniques.
Are there financial incentives for recycling non-PCB ballasts?
Yes, many governments offer tax breaks and grants to encourage recycling. Additionally, selling recovered materials generates revenue.
How can consumers identify non-PCB ballasts for recycling?
Non-PCB ballasts are typically labeled as such. Check product documentation or consult with manufacturers if unsure.
What challenges do recycling facilities face with non-PCB ballasts?
Facilities face challenges like intricate designs, lack of awareness, and the need for specialized equipment.
How does non-PCB ballast recycling contribute to the circular economy?
By recovering and reusing materials, recycling reduces raw material demand and minimizes waste, fostering a sustainable cycle.
Leave a Reply